Both Loctite 242 and 243 are categorized as Blue threadlockers since they have medium strength and can be generally removed with hand tools, without heating.
Loctite 242 is a threaded fastener locking and sealing compound that may be disassembled using basic hand tools. When confined in the absence of air between close-fitting metal surfaces, the product cures, preventing loosening and leakage due to shock and vibration.
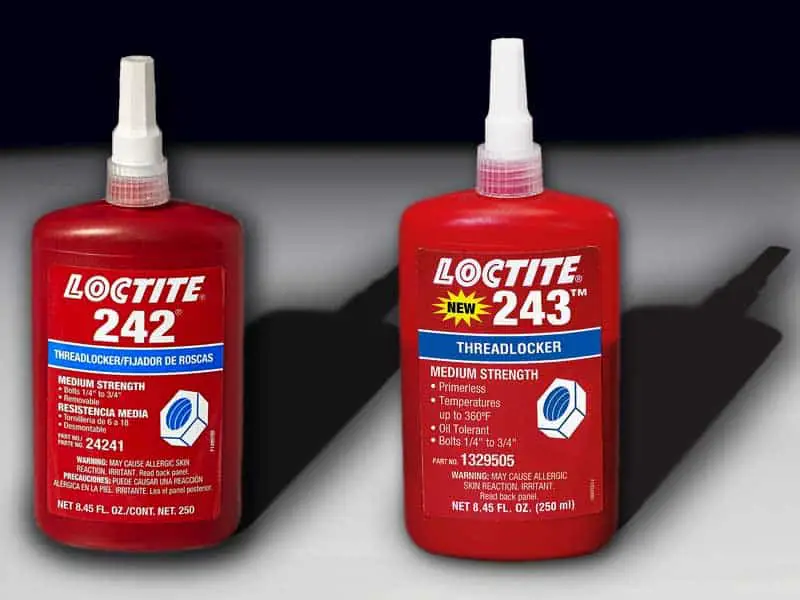
Suitable for usage on less active substrates, such as plated surfaces, where servicing requires disassembly with hand tools. Its thixotropic characteristic prevents liquid product migration following application to the substrate.
Loctite 243 is a threaded fastener locking and sealing compound that may be disassembled using basic hand tools.
The substance cures when confined in the absence of air between close-fitting metal surfaces, avoiding loosening and leakage caused by stress and vibration. The liquid solution’s thixotropic composition prevents movement after application to the substrate. It has a good curing performance.
It operates on both active metals (such as brass and copper) and passive substrates like stainless steel and plated surfaces. This product has a high-temperature rating and is oil resistant.
It can withstand slight contamination from a variety of oils, including cutting, lubricating, anti-corrosion, and protection fluids.
Both Loctite 242 and 243 are similar in terms of being thixotropic (medium viscosity), having medium strength, and could be removed by hand tools but Loctite 243 exceeds its counterpart in terms of performance since it is chemically strong, oil tolerant, and doesn’t need a primer.
Characteristics | Loctite 242 | Loctite 243 |
Color | Blue | Blue |
Odor | Mild | Mild |
Physical form | Liquid | Liquid |
Chemical Type | Dimethacrylate ester | Dimethacrylate ester |
Service Temperature | -54.0° – 149°C | -55.0° – 180°C |
Viscosity | 900 – 1,400 cP | 2150 cP |
Specific Gravity @ 25°C | 1.1 | 1.08 |
Cure | Anerobic | Anerobic |
Secondary Cure | Activator | Activator |
Components | Only one | Only one |
Water Resistance | Yes | Yes |
Require Mixing | No | No |
Technology | Acrylic | Acrylic |
Fluorescence | Positive under UV light | Positive under UV light |
Substrates | Metal: Steel, Metal: Steel – Stainless Steel, Metal: Brass | Metal, Metal: Passive Metal |
Storage Temperature | 8° – 21°C | 8° – 21°C |
Table of Contents
Composition Differences
The most effective components present in both of these threadlockers along with their mass percentages are listed below:
Components of Loctite 242 | Percentage contribution of Total Mass |
Polyglycol dimethacrylate | 60 – 70 |
Oleic acid | 20 – 30 |
Saccharin | 1 – 5 |
Silica, amorphous, fumed, crystal-free | 1 – 5 |
Cumene hydroperoxide | 1 – 5 |
Propane-1,2-diol | 1 – 5 |
Cumene | 0.1 – 1 |
Titanium dioxide | 0.1 – 1 |
Components of Loctite 243 | Percentage contribution of Total Mass |
Tetramethylene dimethacrylate | 10 – 30 |
2,4,6-Triallyloxy-1,3,5-triazine | 1 – 10 |
Propane-1,2-diol | 2 |
Maleic acid | 1 |
Acetic acid, 2-phenylhydrazide | 1 |
Others | 60 |
The components used to formulate Loctite 243 are more advanced than those used in its counterpart, providing it with higher strength, better oil tolerance, and superb durability.
Where are they used?
When it comes to Loctite 242 versus 243, they’re both suitable for medium-strength applications like thread-locking:
- Rocker Studs
- Oil Pans
- Disc Brake Calipers
- Pulley Assemblies
- Valve Cover Bolts
- Lock Washers
- Lock Nuts
- Carburetor Studs
- Hand Tools etc
What is their Thread Size?
Before choosing the best threadlocker, you must first determine the thread size. Service or disassembly will be more difficult if you make a mistake.
Using a high-strength threadlocker in smaller thread sizes may make it more difficult to remove the fastener without breaking the screw.
On the other hand, using a low-strength threadlocker on a larger thread size may limit the adhesive’s effectiveness.
Both Loctite 242 and 243 are used to seal and tighten fasteners with a maximum thread size of M18.
Metal Fasteners Size
The threadlockers are used to attach metal fasteners in a variety of applications, although their size compatibility is restricted, as shown below.
Both Loctite 242 and 243 can be used with metal fasteners with a diameter of 1/4″ (6 mm) to 3/4″ (19 mm).
Strength Comparison
Both these threadlockers are classified as a medium-strength fluid but on a microscopic scale, the strength of Loctite 243 is minutely higher than that of its competitor since it’s a higher version and has a stronger chemical composition which gives it enough boost to beat Loctite 242.
Their Durability
Although both have an equal flashpoint temperature meaning that they are capable of enduring the same amount of heat energy, but the advanced chemical formula of Loctite 243 makes it more durable in comparison to Loctite 242.
Characteristics | Loctite 242 | Loctite 243 |
Flashpoint temperature | 93.3 °C | 93 °C |
Oil Resistance
The biggest advantage Loctite 243 have over its competitor is its greater oil tolerance while Loctite 242 struggle in the oily environment to maintain thread-locking and its weak formula is unable to handle such conditions. Therefore, Loctite 243 is a must choice in assemblies where there is a chance of oil leakage.
Environmental Resistivity
We tested cure for a variable period @ 23°C using M10 zinc phosphate steel nuts and bolts.
Hot Strength
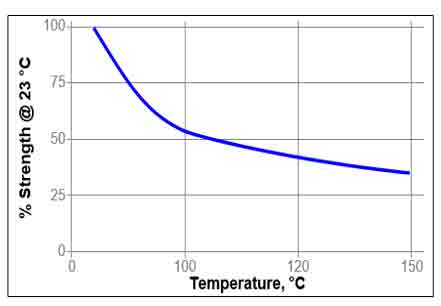
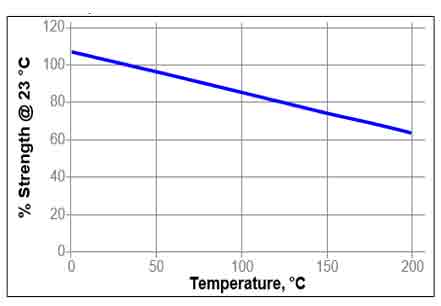
In the case of Loctite 242, the steep fall in percentage strength of cure is observed when the temperature is increased from 23°C to 80°C, after that drop is rather lenient. At the 150°C mark, only approximately 35⸓ strength of the cure is left.
Whereas the cure is formed using Loctite 243, it has a perfect inclined (45°) slope which shows a uniform decrease in the strength of the cure as the temperature increases. Even with this trajectory it only reaches downward till 70⸓ mark @ 150°C.
This clearly shows the higher hot strength of Loctite 243 when compared with its peer.
Heat Aging
Heat Aging refers to the process of the rate of material deterioration due to heat. In the following scenario, the life of the cure is determined by this method which is formulated by different threadlockers. In the subsequent experiment, the strength of cure at 23°C is taken as a standard then multiple cures are introduced to different amounts of fixed temperatures to find the rate of deterioration of these cures.
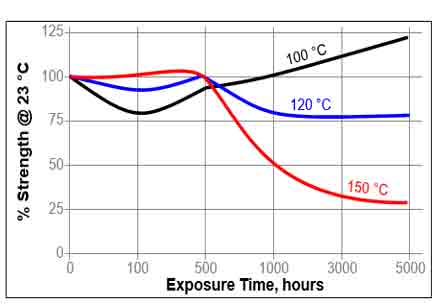
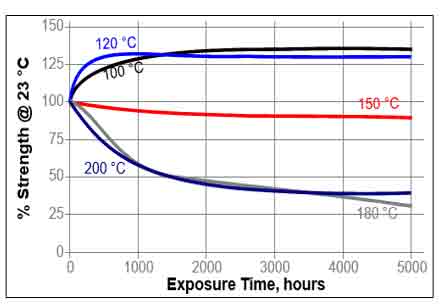
After 5000 hours the Loctite 242 cures have 123⸓ strength at 100°C, 77⸓ strength at 120°C, and 27⸓ strength at 120°C.
On the other hand, the Loctite 243 cures have 135⸓ strength at 100°C, 130⸓ strength at 120°C, and 80⸓ strength at 120°C.
A clear lead of Loctite 243 is again observed through these graphs in terms of life expectancy.
Cold Strength
Loctite 243 has been tested to -75°C (-100 F). Whereas no cold strength tests were performed for Loctite 242, making its rival the winner.
Adhesion Comparison
Cure Speed Vs Substrate
The rate at which the substrate cures is determined by the substrate. The graph below compares the breaking strength of M10 steel nuts and bolts overtime at 23°C to different materials.
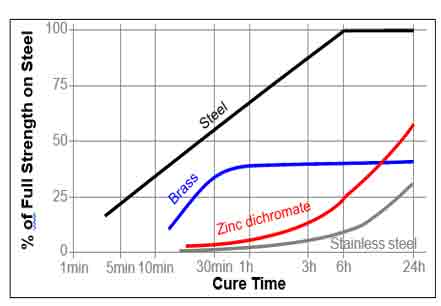
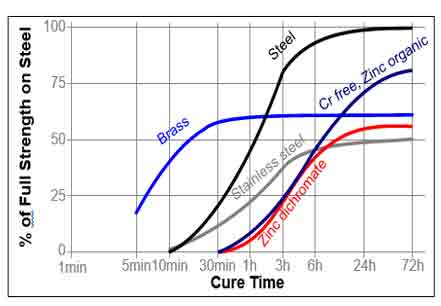
Considering steel, the Loctite 242 cure is formed in mere 6 hours whereas the cure of Loctite 243 takes almost 24 hours to form. But the same could not be said for the same for stainless steel, zinc dichromate, and brass as their cures are formed quickly in the latter one.
Therefore, we can declare Loctite 243 as the winner since it forms cures quickly on multiple substrates except for steel.
Cure Speed Vs Temperature
The temperature will influence the rate of curing on M10 steel nuts and bolts. The graph below demonstrates the breaking strength produced over time at various temperatures.
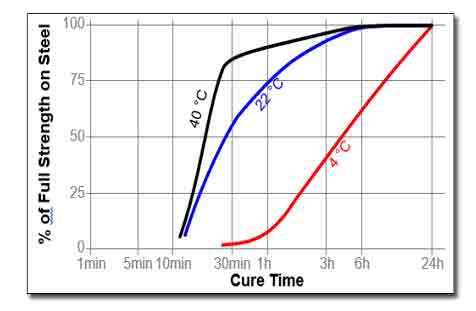
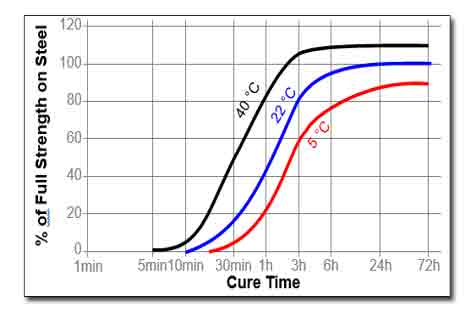
For Loctite 242 the cures forms in 6 hours at both 22° and 40°C while it took 24 hours for it to form at 4°C temperature.
While the cures of Loctite 243 are formed in 3, 24, and 72 hours for 40°, 22°, and 5°C respectively.
Loctite 242 can quickly form a cure in low and medium temperatures whereas the expertise of Loctite 243 lies at higher temperature ranges to finish its job quickly.
Cure Speed Vs Activator
Applying an activator to the surface will improve cure speed if the cure time is too long or there are wide gaps. The graph below demonstrates the breakaway strength acquired over time using Activator 7471and 7649 on M10 zinc dichromate steel nuts and bolts at 23°C.
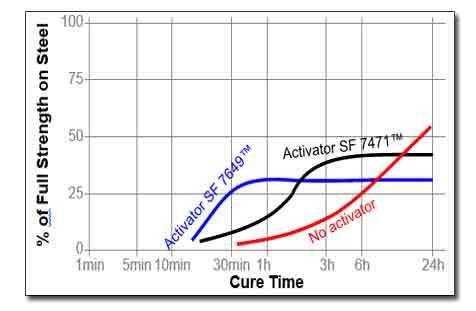
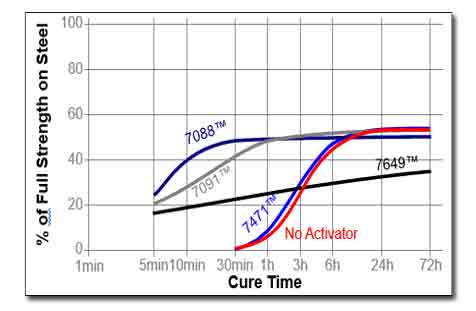
By using activator 7649 the Loctite 242 achieves cure in 1 hour whereas the same is achieved by using 7471 in 6 hours whereas for Loctite 243 both activators help cure in 24 hours.
Using activators with Loctite 242 is clearly more effective than using them with its counterpart.
Chemical/Solvent Resistance
In this test, cures are aged under conditions indicated and tested for the percentage of Initial strength left after 1000 hours
Dissolving Agents | Temperature (ºC) | % of Initial strength left after 1000 hours | |
Loctite 242 | Loctite 243 | ||
Motor Oil | 125 | 100 | 115 |
Unleaded gasoline | 23 | 95 | 95 |
Brake Fluid | 23 | 100 | 110 |
Ethanol | 23 | 95 | 90 |
Acetone | 23 | 85 | 85 |
Water/glycol (50/50) | 87 | 70 | 125 |
Loctite 243 leads in cases where motor oil, brake fluid, and an equal mixture of water and glycol solution are introduced while there is a tie in unleaded gasoline condition. On the other hand, the Loctite 242 is able to have an upper hand only when ethanol was used.
However, it is safe to say that the Loctite 243 has a higher ability to resist dissolving solvents.
Primer Requirement
Priming is used as part of the preparation process for utilizing a thread locker. With the 243, this is no longer needed. However, when binding two inactive techniques, primer is a must required.
The Loctite 242 does need a primer which is why the 243 is the better option.
Tools needed for removal
- Utility knife
- Damp cloth
- A blowtorch
- Heat-resistant safety gloves
- Safety glasses
- A wrench
Setting and Curing Time Difference
Both thread lockers dry in about 10 minutes and cure in about 24 hours. For steel, these numbers are more prevalent but on less active metals, it may take a little longer.
Both adhesives cure a solvent-resistant, non-flammable solid that also has the ability to wick moisture away.
Method of Usage
- For Assembly
- Clean all surfaces (external and internal) with cleaning solvent and let it dry for optimal results.
- Spray all threads with Activator 7471 or 7649 and leave to dry if the material is an inert metal or if the cure speed is too slow.
- Before using, give the product a good shake.
- Allowing the tip to touch metal surfaces during application will cause the product to clog in the nozzle.
- For Thru Holes: Several drops of the product should be applied to the bolt at the nut engagement point.
- For Blind Holes: Several drops of the substance should be applied down the internal threads to the hole’s bottom.
- For Sealing Applications: Apply a 360° bead of product to the male fitting’s leading threads, leaving the first thread unaffected. To completely fill the spaces, force the substance into the threads. Adjust product quantity as needed for larger threads and voids then apply a 360° bead of product to the female threads as well.
- Assemble the pieces and tighten as needed.
- For Disassembly
- Using basic hand tools, remove the item.
- In the rare case where hand tools fail due to high engagement length, apply targeted heat to the nut or bolt at around 250 °C. While the item is still hot, disassemble it.
- Clean-up
A combination of soaking in any solvent and mechanical abrasion, such as with a wire brush, can be used to remove the cured product.
Limitations
- Plastic and thermoplastic materials should not be utilized with them.
- They should not be utilized in environments where there is a lot of oxygen.
- They should not be used as a barrier against chlorine and other strong oxidizing chemicals.
- They aren’t food-grade adhesives at all.
Applications
Loctite 242 is commonly used in alternators, water pumps, and various types of valve covers in automotive applications. Tow motors and most home mechanical parts, in particular, benefit from regular thread locker use. Lawnmowers are an excellent example of a machine that may be used to reduce vibrations and noise.
In the case of Loctite 243 oil pans, disc brake calipers, pulley assemblies, rocker studs, and rocker adjustment bolts are all at the top of the list. The same applications that were submitted for the 242 are also eligible for the 243.
Packaging
Both thread lockers are packaged in the same red bottle that the company utilizes to distinguish itself from its competitors. The liquid within these red Loctite bottles, on the other hand, is always blue for these two. The medium-strength adhesive comes in three forms: liquid, tape, and a glue stick.
Quick Summary
- Both are blue-type threadlockers whereas Loctite 243 is the higher version of 242.
- Loctite 243 is a slightly higher strength threadlocker comparatively.
- The chemical composition of Loctite 243 is much stronger than that of its rival.
- Both are made for medium-strength applications.
- Both are compatible with the same thread and metal fasteners size range.
- Loctite 243 has higher strength and durability along with oil tolerance.
- Hot strength, aging resistance, and cold strength of Loctite 243 are also higher.
- Loctite 243 can bond with different substrates at higher temperatures while Loctite works well at medium and low temperatures and has good chemistry with the activators as well.
- Loctite 243’s ability to resist different solvents is higher than its competitor.
- Loctite 242 needs a primer while 234 does not.
- Both have similar methods of usage, tool requirements, packaging, limitations, and setting time.
- The price of 242 is slightly on the lower edge.